When Is a Laser Scan Necessary?
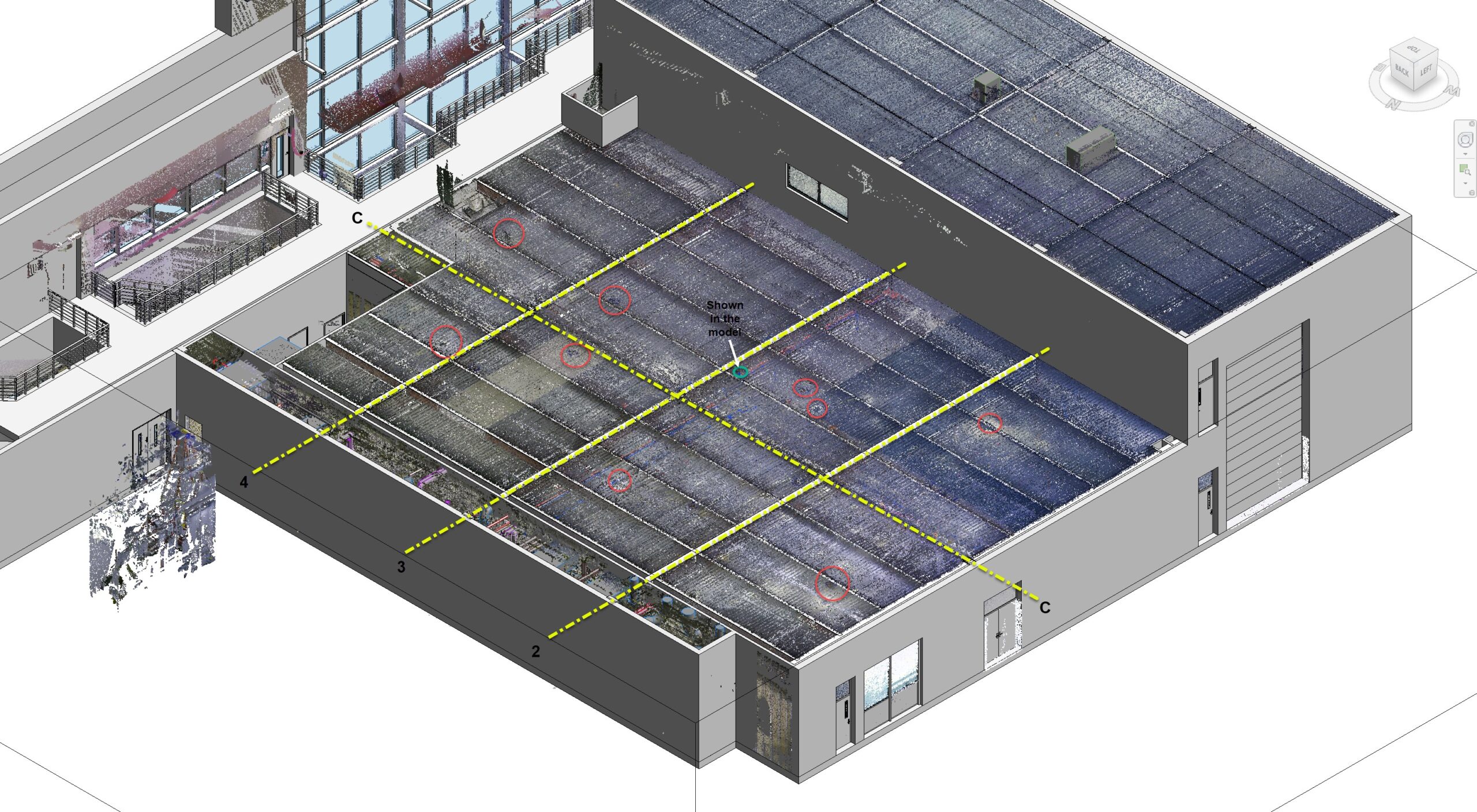
Situation
During a lab-to-cleanroom conversion project in Austin, Flintco Senior Superintendent Rod Nelson noticed a discrepancy. The structural steel at the ceiling depicted in the plans and design model didn’t match the visual as-built condition of the building. The model showed a flat roof. Rod saw something different.
“When I was looking at the model on my iPad, the steel didn’t look right,” Rod said. “I compared what I was seeing to the as-builts and sent grid line dimensions of the ceiling to our Virtual Design and Construction (VDC) team to help verify what I was seeing in the field. The dimensions I sent matched what they had. Together with the design team and owner we decided to laser scan the space to eliminate any doubt.”
Left undetected, this variance would have triggered a cascading and compounding effect of negative outcomes to the steel fabrication, mechanical equipment installation (headroom clearances), how the air handlers would sit on the roof, schedule delays, cost, and the potential for increased safety risks due to rework.
After getting the call from Rod, Flintco VDC Senior Manager Bhavna Biyani initiated a laser scan of the space, which confirmed the existing roof had a 1′ 7″ slope, while the design model showed a flat roof.
“We laser scanned the space and converted that data into an additional model,” Bhavna said. “For better navigation, we used the scan-to-BIM model that Rod was looking at against the new steel. That was the comparison he saw; when I double-checked in the model with the laser scan turned on we had all the information we needed.”
Rod’s ability to spot discrepancies in the field against plans or a BIM model comes with experience. Addressing issues immediately by deploying the right technology (laser scanning in this instance) illustrates a Flintco differentiator. This combination of results-driven action also speaks to the capability of Flintco’s Construction Support Services (CSS) Department, and our overall approach to preconstruction services. Flintco is continuously identifying, vetting, and implementing new technology with a dedicated team of in-house technologists, architects, and construction subject matter experts to bring owners the best value and deliver a satisfying construction experience.
Laser scanning captures millions of measurable data points of the target environment that can be integrated with 3D models. It is used to verify existing conditions, flatness of concrete, beam deflection, true installation of elevators, and low point verification for drains, among other tasks. Its primary purpose during renovations is to ensure the accuracy of existing conditions.
The point cloud data generated by a laser scan is robust and can be somewhat difficult to navigate. Flintco’s team of VDC experts help bridge that gap by identifying point cloud clusters that represent different design elements (a beam, for example), and then translating that element into a shared Revit model for easy reference by the entire team. Getting the transition from the point cloud to the model is a critical step.
Flintco started using laser scanning as early as 2013. In 2018, the company began acquiring laser scanning equipment and established an in-house department to operate it. Flintco has a mobile team within CSS that supports each of our eight offices. The company also maintains a network of vendors who provide laser scanning services.
“In most instances, the design team verifies the as-builts, which informs their models and plans,” said VDC Director Kevin Bromenshenk. “But we always consider ourselves partners with the design team and act accordingly. In this instance, we had the technology at our disposal, and knew the buck stops with us as to means and methods. Being proactive and conducting a laser scan early before completing the programming of this cleanroom conversion was like stopping a snowball from getting bigger.”
Other examples where Flintco’s VDC team has used laser scanning to prevent a discrepancy from snowballing include:
- Ensuring precise locations for building corners during excavation so that shoring is placed correctly, juxtaposed to drilled piers and pier caps.
- Verifying that a load bearing, concrete column is true – the naked eye can be deceiving – and in its precise location before making the next pour so each column lines up exactly as it should.
Laser scanning is a highly effective means to verify existing conditions, proactively identify issues, and provide the owner the best value. Within four hours, it is possible to scan 40,000-50,000 SF covering multiple floors. While it requires upfront investment (approximately $2,500 per day depending on the project), it more than pays for itself by avoiding costly delays later during construction.
At the start of every project, Flintco project teams discuss different technology solutions with owners, the design team, and trade partners. The process is transparent and collaborative with everyone informed and on board from the start. Trade partners know what to account for during buy out and owners are confident costs are being allocated properly. And the design team knows we always have their back.